STEAM Honors Design and Development Senior Capstone Project
SUMMARY
The main goal of my project was to find an effective way to cut down on the amount of single use gloves used in the food industry. My original ideas were ineffective and I found some models worked better than others. My first prototype had traditional drawers, but this only allowed one side of the glove to have full exposure to the UV-C light and didn't allow multiple gloves to be cleaned at the same time. My final product that I presented at the expo had 3-D printed holder that allowed the gloves to get full exposure to the light and could clean four pairs at a time. There were many other changes I made like adding pegs at the bottom and stick pads to prevent it from sliding. I also laser cut holes in the bottom for good ventilation and used drawer sliders to make everything glide smoothly. I went through several different variations of everything including the drawer knobs which originally started out as handles.
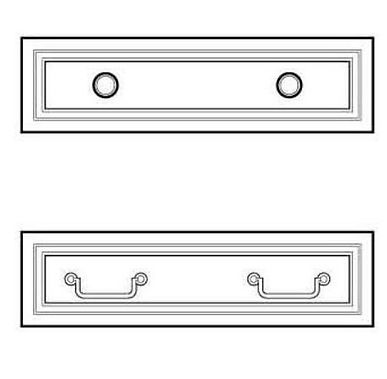
MY MAIN CHALLENGES
1. Deciding on a model:
Figuring out how I wanted to solve this problem was the hardest part for me. I had so many different ideas I wanted to try out and I spent a lot of time just trying to decide on what concept would be the most effective.
2. Getting the box to stay together:
I laser cut the acrylic to have slats that fit each other giving the joints extra support, but I still needed a way to hold the box together. At first I used tape, until I found a glue that could chemically bond the plastic. However, this took many coats and was pretty messy.
3. Lining up the drawer sliders:
In order to get the drawer sliders secured in place I had to drill holes in the side of the box for the bolts. While drilling the hole was easy, making sure it was in the right spot was not. I had to re-drill all the holes in the left side because I lined them up wrong.

BENEFITS
1. New Skills:
This project required me to do a lot of 3-D printing, laser cutting, and experimentation. I learned how to prepare a petri dish and how complex simple parts can be like drawer handles.
2. New Connections:
The professional review and expo night gave me a lot of new connections with people. I met people from Medtronic, electrical engineers, and even a fellow Lifetime worker. It was really exciting to hear their feedback and I hope keep in contact with them.
3. Encouragement:
I wasn't really sure what to expect with my final product, but everyone that I talked to seemed really impressed. This made me feel really proud and excited about all the work that I did. I was worried about the real world application of this more than anything, so it was reassuring to hear how others could see something like this in a business.
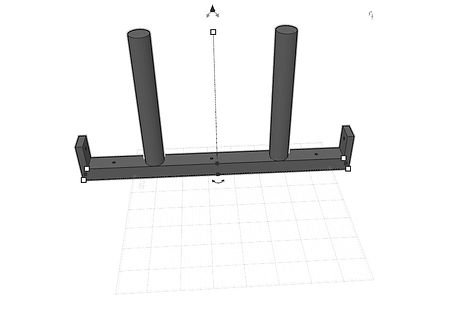
FUTURE
Even though I am technically done with the STEAM program I hope to continue working on this project. I would love to present it to a business owner in the food industry to see where this product falls short. Another future goal of mine for this project is to figure out how expensive producing something like this would be. Because gloves are so inexpensive, making the product cheap would be critical in influencing businesses to purchase it. Lastly, I would be interested in figuring out how much energy this product uses to ensure that it is actual benefiting the environment.
The last four years in STEAM have continuously challenged me to problem solve and learn "unconventional" skills. I now know how to solder, use a micro bit, create basic circuits, laser cut, 3-D print, and use a plethora of different software's. STEAM also gave me a lot of different passions that I have pursued outside of class like learning about how homes can be designed to conserve energy by using concrete flooring that absorbs heat. I plan on continuing to learn more and develop both the interests and skills that the STEAM program has given me.